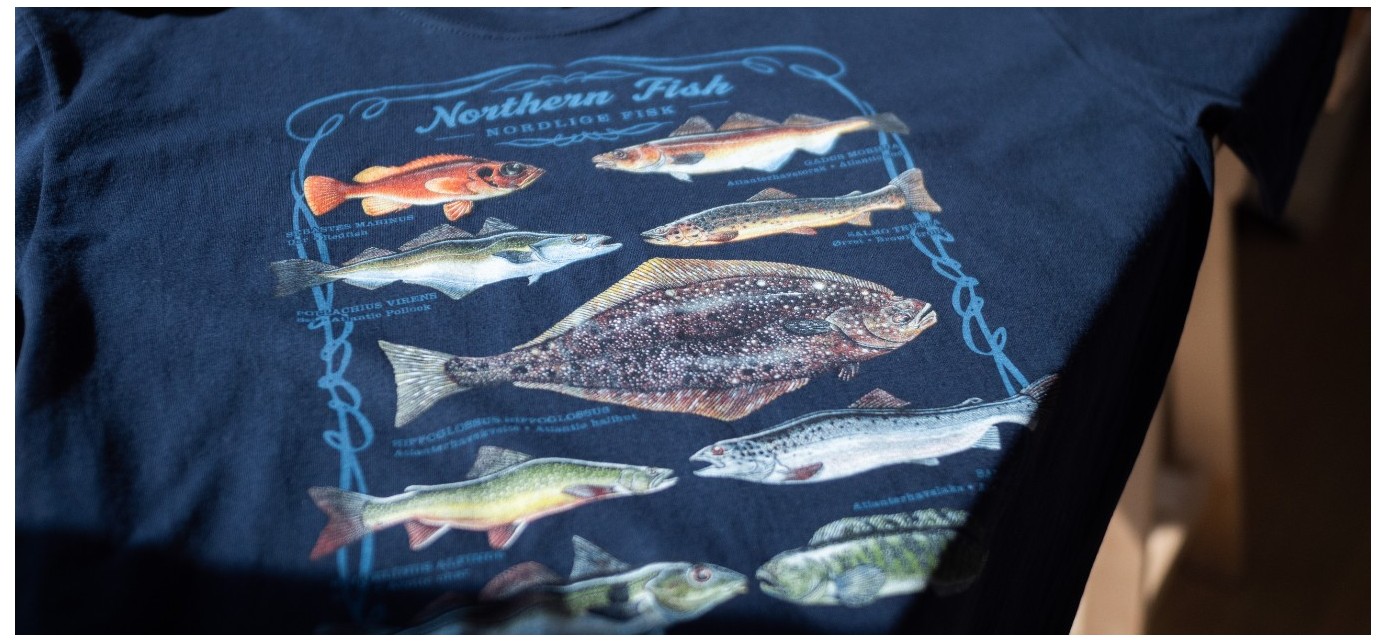
Screen printing - The most popular marking methods
Screen Printing: The Most Durable Garment Decoration Technique
This is the first article in a series where we will briefly introduce you to the most popular garment decoration methods available on the market. In each article, we’ll discuss the strengths and weaknesses of the featured technology, focusing on essential information for designers preparing artwork. We’ll also share tips on how to care for prints. Believe it or not, some prints can last for decades! The strongest candidate for the title of the most durable technique is screen printing – the hero of today's article.
Also known as serigraphy or silkscreen printing, screen printing is one of the oldest printing techniques that remains largely unchanged to this day. Its origins date back to the mid-10th century. Although the technique was initially developed in China, the Japanese made significant contributions to its development by creating paper stencils called ‘katagami.’ These stencils were used to decorate kimonos. Screen printing arrived in Europe relatively late, at the end of the 18th century, but did not gain much popularity due to the limited availability of materials needed for mesh production.
This all changed in the early 20th century, and in the 1960s, screen printing experienced a real boom. Even Andy Warhol embraced the appeal of screens, squeegees, and ink. One of his most famous works, the Campbell’s Soup can, was reproduced using this technique.
The relatively simple process and accessibility of materials made screen printing a favorite technique among alternative artists. It was used to reproduce zines, create album covers, and decorate clothing. The seemingly rough aesthetic of this technique became a hallmark of the DIY (Do It Yourself) movement in alternative cultural circles.
Screen printing is perhaps the most versatile and accessible printing technology. It can be used on textiles, plastics, paper, and even glass. However, today it’s most commonly used for decorating promotional clothing, with other fields increasingly relying on pad printing, digital printing, offset printing, and engraving.
Technology
So, how is it done?
The first step is to create a printing form, usually a fine metal or fabric mesh stretched over a frame. A photosensitive emulsion is applied to the mesh and then exposed to light, creating a stencil on the screen (sound familiar? Think of the Japanese katagami!). Ink is then pushed through the screen using a squeegee or an automated carousel. After printing, the garment is cured in a heat tunnel to set the ink. And that’s it! Just like Japanese kimonos in the 10th century, we’re decorating your T-shirts nearly eleven centuries later! Additionally, we can enhance the print with puff, glitter, gel, or 3D effects.
Who is Screen Printing For?
When should you use screen printing?
Screen printing is ideal for medium and high-volume orders. The cost of preparing the printing form can make individual or low-quantity orders more expensive per unit. Screen printing also has some limitations. Each color is typically applied in a separate pass, which means a printing form must be prepared for each color. Therefore, screen printing is best suited for designs with a limited color palette – the more colors, the longer the process and the higher the cost. It’s recommended to use this technique for designs with 1, 2, or 3 colors.
Screen printing is commonly used on cotton, polyester, and polyester-cotton blends. It’s ideal for decorating T-shirts, hoodies, and reflective vests.
How to Prepare Artwork for Screen Printing
Screen printing is typically done with plastisol or water-based inks, with colors selected according to the Pantone Matching System (PMS). The Pantone system, developed by Pantone Inc. in the USA, provides a standardized color system used worldwide. Colors are designated by a number (e.g., 2352) with additional indicators for fluorescence, metallic effects, etc. The basic Pantone system covers 1,761 colors created by mixing 18 base pigments (including black and white).
Some print shops may request files with separations. This simply means preparing a separate file for each color. The artwork is best prepared in vector format. When sizing elements in the design, always consider the dimensions of the garment being decorated. If possible, include a visualization with the production file. If specific distances from the hem or collar are required, indicate these in the visualization file to help the print shop and avoid delays.
How to Care for Screen-Printed Garments
How long will it last?
Although screen prints are some of the most durable, a few washing tips can help them last even longer:
- Always wash garments inside out. This prevents the print from rubbing against the drum of the washing machine, extending its lifespan.
- Wash at a maximum of 40°C (104°F) and avoid tumble drying – high heat can cause the fabric to shrink, distorting the print.
- Avoid using bleach, stain removers, and other chemicals – they can react with the inks.
- Do not iron directly on the print – this could damage not only your favorite T-shirt but also your iron! If you must iron, do so on the reverse side at a low temperature.
For more details on popular printing methods, check out our article on Digital Printing (DTG) from our series "The Most Popular Printing Methods."